Direktmetallisierung von Kunststoffoberflächen
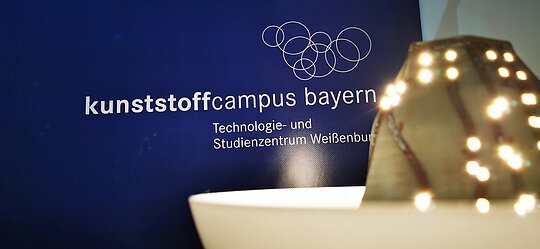
- Titel des Vorhabens:
"Entwicklung von metallisierten 3D-Grundkörpern zur Aufbringung von elektrischen Leiterbahnen auf beliebigen Freiformflächen ohne nasschemische Prozesse zur Herstellung von LED Lampen"
-
Förderkennzeichen: ZF4647001LT8
-
Kooperationspartner: DOTLUX GmbH
- Laufzeit: 01.01.2019 - 31.12.2021

Ausgangslage und Marktbedarf:
Traditionelle Lampen werden immer mehr durch moderne Lichtquellen auf Halbleiterbasis ersetzt. Sie zeichnen sich durch eine deutlich höhere Energieeffizienz und Leistungsfähigkeit aus. Dabei haben sich die Lichtemittierenden Dioden in den letzten Jahren zu einer breit verfügbaren Alternative für fast alle Beleuchtungslösungen entwickelt. Im Vergleich zur klassischen Glühlampe besitzen die LEDs eine deutlich bessere Öko-Bilanz, schonen die Umwelt und sparen somit Strom und Geld ein.
Die Schaltungsträger vieler LED-Lampen basieren derzeit auf einem 2D Layout, wie zum Beispiel die Retrofit LED Straßenlampe (siehe Abbildung) der Firma Dotlux GmbH im bayerischen Weißenburg. Zur Erzeugung von hohen Abstrahlungswinkel müssen mehrere Leiterplatten in aufwendigen Montageschritten auf einem Sockel kreisförmig ausgerichtet werden. Das Schaltungslayout sowie die dazugehörigen Bauelemente (LEDs, Widerstände, Dioden, usw.) werden hierzu jeweils auf separate 2D-Leiterplatten aufgebracht. Zur Ableitung der entstehenden Wärme müssen aktuell die einzelnen Leiterplatten mithilfe von Wärmeleitpaste auf einen zentralen Kühlkörper montiert werden. Der Herstellungsprozess der benötigten 2D Leiterplatten ist aufgrund des Einsatzes von Ätzchemie nicht umweltfreundlich zudem ist der gesamte Montageprozess der Lampen insgesamt zeitaufwendig.
Mit einem innovativen Trockenfertigungsverfahren, der sogenannte Direktmetallisierung, werden mit der Kombination aus Spritzguss, Siebdruck sowie der Laser- und Plasmatechnologie elektronisch leitfähige Bahnen direkt auf thermoplastische Oberflächen aufgebracht. Bei diesem Prozess werden keine gesundheitsschädlichen Produkte wie z.B. Ätzmittel (Eisen-3-Chlorid, Aminiumpersulfat) bzw. Kupfer zur Aufbringung der Leiterbahnen benötigt. Die Bauteile werden zudem meist aus rezyklierbaren Thermoplasten hergestellt und sind somit unkritisch bei der Entsorgung.
Definition geforderter Eigenschaften
Gemeinsam mit dem Projektpartner wurden die Eigenschaften des Materials des Lampenkörpers definiert, wobei verschiedene Faktoren berücksichtigt werden mussten. Einerseits sollte neben der guten Compoundierbarkeit der Rohmaterialien auch die Möglichkeit der Beschichtung mit einer Haftung von mindestens 1,1 N/mm erreicht werden. Auf der anderen Seite sollte das Material elektrisch isolierend, aber dennoch eine hohe Wärmeleitfähigkeit sowie Temperatur- und Chemikalienbeständigkeit aufweisen. Ebenso wurden Möglichkeiten der Recyclingfähigkeit in Betracht gezogen.
Materialauswahl, Compoundierung und Spritzguss von Prüfkörpern
Zu Projektbeginn wurden im Rahmen einer Masterarbeit die folgenden thermoplastischen Materialien im Spritzgussverfahren verarbeitet und metallisiert:
- HDPE (Silonverbindungen Taborex - Ta1108)
- LDPE (DOW640C Natur)
- PA6 (TechnylC206 Natur)
- PA6 (Durethan BKV 15H 1.0+ 30. + 20% Al2O3 + 15% Glasflocken)
- PA66
Die Untersuchung der Polyamide zeigte aufgrund der gut zu beschichteten Oberflächen hinsichtlich der Metallisierung zunächst die besten Ergebnisse. Um die Wärmeleitfähigkeit zu verbessern, wurde Al2O3 ausgewählt, um die Polymermatrix zu verstärken und die niedrige Wärmeleitfähigkeit der Polymermatrix zu verbessern. Aluminiumoxid dient hierbei zusätzlich als Flammschutzmittel.
Abgeleitetet aus den Untersuchungen mit LDPE, PA6 mit Al2O3 und PA6 natur sowie weiterer detaillierter Recherche fiel die weitere Materialauswahl auf ein Polyamid 6 (PA6) bzw. PA66 und ein Polybutylenterephthalat (PBT) mit jeweils Aluminiumoxid (Al2O3) und einem Glasfasermehl als Füllstoff. Diese Compounds wurden mittels Doppelschnecken-Extruder zu rieselfähigen Massen verarbeitet. Anschließend wurden daraus zweidimensionale Prüfkörper via Spritzguss hergestellt.
Beschichtung via DDM und Bestückung von 2D-Körpern
Die am Technologiezentrum vorhandene Plasmaanlage zur Digital Direct Metallization (DDM) besitzt einen integrierten 6-Achsroboter. Dies ermöglicht die ortsaufgelöste Beschichtung der Prüfkörper. Beim DDM-Verfahren wird das Kupferpulver durch einen Plasmastrahl geschmolzen und in Richtung der Werkstückoberfläche beschleunigt.
Im Anschluss wurden diese beschichteten Proben mit LED’s bestückt und erfolgreich auf ihre elektrische Leitfähigkeit sowie ihren elektrischen Widerstand untersucht. Ebenfalls war die Haftfestigkeit der erzeugten Kupferschichten zu analysieren. Bei dem Vergleich der verschiedenen Compounds fiel die Entscheidung hinsichtlich Leitfähigkeit und Haftfestigkeit trotz der etwas geringeren Wärmeleitfähigkeit im Vergleich zu PBT und PA66 auf PA6 mit 30 Gew.-% Glasfaserfüllstoff.
Um dieses Material auch dreidimensional auf ihre Eigenschaften zu untersuchen, muss ein entsprechendes Filament für den 3D-Druck hergestellt werden.
Prüfung der Beschichtung und Optimierung Prozessparameter
Für den späteren Einsatz der Lampenkörper in Beleuchtungsanlagen muss die Haftfestigkeit der Beschichtung über den Produktlebenszyklus gewährleistet sein. Zur Validierung wurden Probekörper verschiedenen Prüfungen unterzogen:
- mechanische Prüfung
- Temperatur-/Feuchtelagerung
- Beschleunigte Alterung durch Bewitterung
- visuelle Begutachtung
Die Ergebnisse zeigten, dass sich die Optik der Beschichtung aufgrund von Oxidierung zwar verfärbt, aber keine Verschlechterung der elektrischen Leitfähigkeit oder höherer Widerstand auftritt. Neben den Untersuchungen wurde die Beschichtung soweit optimiert, dass sich auf dem Grundkörper eine nahezu identische Schichtdicke der Kupferleitbahn einstellt. Dies stellt die Basis für eine gleichbleibende Stromtragfähigkeit für die noch zu bestückenden LED´s dar.
Filamentherstellung und Prototypenbau mittels additiver Fertigung
Für den Prototypenbau wurde ein Filament von dem eigencompoundierten Material hergestellt. Hierbei konnte die Erfahrung und Unterstützung des Pappenheimer Kunststoffmaschinenvertrieb (PKV) genutzt werden, um den geforderten konstanten Filamentdurchmesser von 1,75mm für das Fused Filament Fabrication (FFF) Verfahren zu realisieren. Bei der Herstellung der Prototypen lag die Herausforderung auf der Oberflächenrauigkeit der hergestellten Bauteile, damit anschließend eine optimale Haftung der 3D-Beschichtung erreicht werden kann.
Maskierung und Beschichtung der 3D-Grundkörper
Um das gewünschte Schaltungslayout auf den 3D-Körpern mittels Plasmabeschichtung aufzubringen, wurde eine entsprechende Maskierung aus Stahl mit Hilfe des addtiven Fertigung am Technologiecampus der THD in Cham hergestellt. Nach Programmierung des integrierten KUKA-Roboters für die dreidimensionale Beschichtung konnte das durch den Partner Dotlux entwickelte Leiterbahnen-Design auf dem Grundkörper aufgebracht werden. Hierbei wurden mehrere Lampenkörperformen für verschiedene Einsatzgebiete mit jeweils angepasstem Leiterbahn-Layout umgesetzt. Durch systematische Variation der Prozessparameter Stromzufuhr, Gasdurfluss, Förderrate oder Abstand zwischen Düse und Substrat wurde eine möglichst widerstandsarme und elektrisch leitfähige Beschichtung erreicht.
Bestückung und lichttechnische Überprüfung
Die Bestückung der 3D-Körper stellte einige Herausforderungen bereit. Unter anderem die LEDs an den genauen Kontaktpositionen anzubringen oder die geeignete Löttemperatur zu finden ohne den Grundkörper zu stark zu beeinträchtigen. Nach erfolgreicher Aufbringung und Kontaktierung der LEDs, konnte die lichttechnische Überprüfung durch den TÜV erfolgreich durchlaufen werden.
Für weitere Informationen sprechen Sie uns an!!!
M.Sc. Dominik Weiß
- dominik.weiss@th-deg.de
- +49(0) 9141/874669-214
Prof. Dr. Dmitry Rychkov
- dmitry.rychkov@th-deg.de
- +49(0) 9141/874669-201